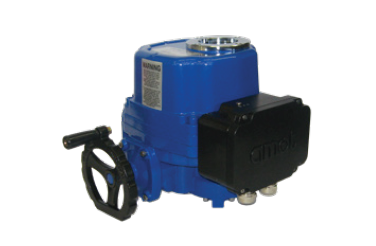
Power
- Key Features & Benefits: High vibration resistance Self-locking with minimal backlash in transmission - prevents valve movement due to flow Auxiliary limit switches for user connection Manual override fitted as standard - valve can be operated in event of power failure Two torque switches - provide protection in event of actuator overloading Improved Duty Cycle
EB100- High vibration resistant, DNV approved and DIP switches
For the electrically operated valves, a number of actuator options are available, which use an electric motor that rotates in either direction in response to the ON-OFF signals received.
The motor drives a gearbox connected to the rotor shaft and turns the valve rotor clockwise or counter-clockwise, a maximum of 90 degrees. At the end of travel, limit switches are incorporated to isolate the electrical supply to the motor when the valve rotor has reached either end of the rotation. A feedback hall sensor is available on some actuators, providing position indication to the control system.
Most actuators are powered by an electric motor driving a worm-type gearbox. The worm gearbox prevents reverse drive due to the forces generated by fluid flow. A thermal cutout is fitted preventing overheating. Limit switches at each end of stroke disconnect motor power when end stroke is reached. These can also be used for remote indication.
See page 12 for more information on the electric actuator options